Around the world, wastewater treatment plant operators face the same conundrum: what to do with the biosolids that they spend so much effort removing from the wastewater.
Some apply it to land. After all, this organic sludge is rich in nutrients. However, it can also contain a cocktail of different contaminants, from household cleaners, paint and solvents to industrial chemicals.
Other treatment plants incinerate their biosolids. That’s a very expensive undertaking, since drying and burning such a wet material requires huge amounts of energy. It also produces significant volumes of greenhouse gases.
Guelph’s Savron Solutions is developing a radically different solution: smouldering combustion.
Yes, wet material is combustible
Smouldering is a form of combustion that creates heat but not flames. (Think of charcoal briquettes in an old-fashioned barbeque.) But can you smoulder something wet? The answer is yes — and Western University’s Dr. Jason Gerhard proved it in 2005.
Back then, the civil engineer was a professor at the University of Edinburgh, investigating how to remediate soils contaminated by oil leaks. One day, he was chatting over coffee with a fire researcher from the lab next door.
“We started talking about this thing called smouldering, which I didn’t know anything about,” Gerhard recalls. A crazy thought struck him: could he use this process to tackle soil contamination? Although it took several years to work out all the details, he succeeded.
That’s when Savron came into the picture. A division of Geosyntec Consultants, Savron was created to turn Gerhard’s breakthrough into a commercial technology. The result was STARx.
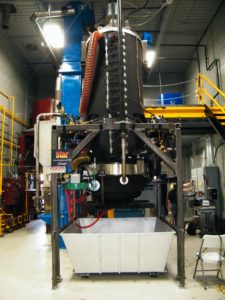
Savron’s STARx biosolides smouldering technology. Copyright: Savron Solutions
The STARx system
There are four things required for successful smouldering. You need a fuel. In the case of soil remediation, that’s the contaminant you’re trying to get rid of. You need oxygen, which STARx provides by blowing air through the fuel. You need enough heat to get the reaction started. In the case of STARx, that’s achieved with a heating element.
Finally, you need a porous matrix — something that allows air to circulate, provides lots of surface area where smouldering can occur and has enough thermal mass to store heat and then radiate it back, keeping the reaction going. STARx uses sand because it is cheap and readily available.
If you’ve got all the ingredients in the right proportions, the reaction becomes self-sustaining and you can switch off your heat source. “We’ve shown it’s incredibly safe and totally controllable,” says Gerhard.
Turning the focus to biosolids
Smouldering combustion works effectively for soil remediation. But could the same approach work on biosolids? After all, they contain far less stored energy than oil-soaked soil, and they contain far more water.
Gerhard’s student, Tarek Rashwan, started experimenting in the lab and came up with highly promising results. Now, with the help of an Advancing Water Technologies (AWT) Program grant from the Southern Ontario Water Consortium (SOWC), Gerhard and Savron are figuring out how to scale up the technology.
To keep the size of the system as small as possible, they’re testing how much they can reduce the ratio of sand to biosolids. They’re looking at the emissions produced, so that they can add scrubbing systems, if necessary.
They’re also investigating whether it’s possible to recover phosphorus from the ash and sell it as fertilizer, creating a valuable revenue stream for treatment plants.
That information will allow Savron to create a viable commercial system.
“What this research is really going to tell us is what are the operational limits and what are the range of conditions necessary to treat biosolids,” says Gavin Grant, Savron’s operations manager.
AWT funding fills a crucial gap
According to Gerhard, SOWC’s funding helps them bridge the gap between the lab bench and the marketplace. “Someone has to invest in proving the technology at a pilot scale,” he explains. “When it works, everyone gets excited and they starting lining up to do it on their site. But it’s a very conservative industry and they want to see somebody prove it first. That’s why the AWT grant is so important.”
The funding has made it possible to buy sampling equipment and to rent space in a specialized facility for large-scale experiments. It has also allowed Gerhard to hire two graduate students and six undergraduate students, who are conducting the testing.
If the project is successful, it promises to transform biosolids treatment. As an alternative to incineration, it could dramatically reduce the amount of energy required, cutting costs and greenhouse gas emissions. And as Gerhard’s research shows, smouldering combustion also kills disease-causing microorganisms and breaks down contaminants.
As a result, this could open up a new global market for Savron, growing their business and creating more jobs here in Ontario — perhaps for some of the students currently being trained in Gerhard’s lab.
“Our goal is just to find a better way to do things,” Grant says — a goal made possible through the AWT-funded collaboration with Western.